Lamborghini i włókno węglowe. Ponad 35 lat historii.
Mocną stroną działalności firmy Automobili Lamborghini jest ciągły rozwój technologii i szerokie zastosowanie lekkich materiałów z włókna węglowego. Ciągłe badania i innowacyjne podejście pomogły marce Lamborghini znajdować się na czele producentów tego sektora przez ponad 35 lat. Oto 12 kluczowych momentów tej niezwykłej historii.
1983
Lamborghini po raz pierwszy zaczyna stosować i rozwijać technologię włókna węglowego. Nowy dział w firmie nazwany „Esperienza Materiali Compositi” (znany jako E.Co) powstał dzięki know-how pochodzącemu z Seattle. Tam opracowano jedne z pierwszych komponentów z włókna węglowego i kevlaru, które zastosowano w Boeingu 767. Powstaje wówczas pierwszy prototyp nadwozia z włókna węglowego. Znany jest on jako Countach Evoluzione. Jest to pierwsze zastosowanie materiałów kompozytowych przez Lamborghini i absolutne pierwsze w projekcie samochodu drogowego.
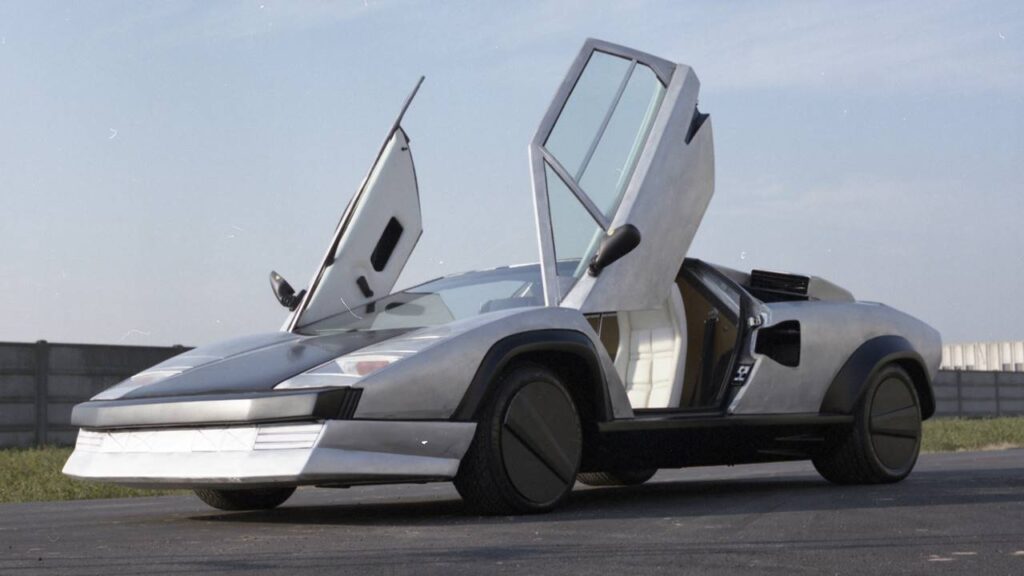
2007
Nawiązanie ścisłej współpracy z Uniwersytetem Waszyngtońskim to ważny kamień milowy w historii kompozytów w Lamborghini. Niektóre aspekty rozwoju technologii RTM poza autoklawem powierzono amerykańskim naukowcom. Tam powstała technologia, którą ostatecznie wykorzystano do konstrukcji monokoka przyszłego Aventadora.
W 2007 roku w Centrum Badawczo-Rozwojowym, obecnie nazywanym „Centrum Rozwoju Kompozytów”, powstaje dział, który koncentruje się na badaniach nad innowacyjnymi materiałami oraz opracowywaniu nowych koncepcji i technologii zastosowań włókien węglowych.
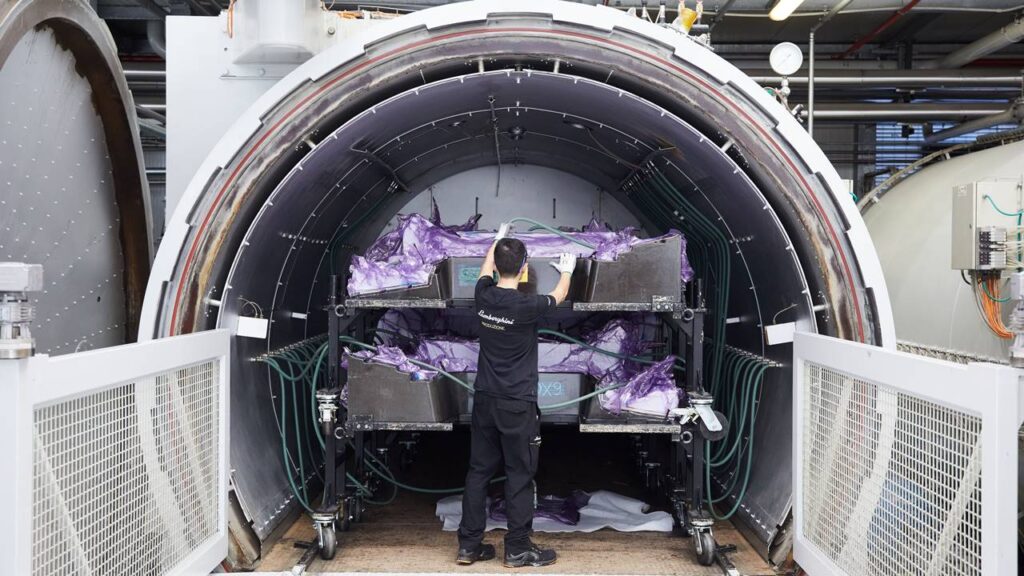
2008
Podpisanie pierwszej umowy o współpracy z Boeingiem w celu zbadania zachowania się materiałów kompozytowych podczas zderzeń. Badano także wytrzymałość monokoku Aventadora. Automobili Lamborghini zaczyna wdrażać technologie materiałów kompozytowych, procesy oraz metody symulacji wprost z przemysłu lotniczego i kosmicznego. Robi to jako pierwszy producent z branży motoryzacyjnej,
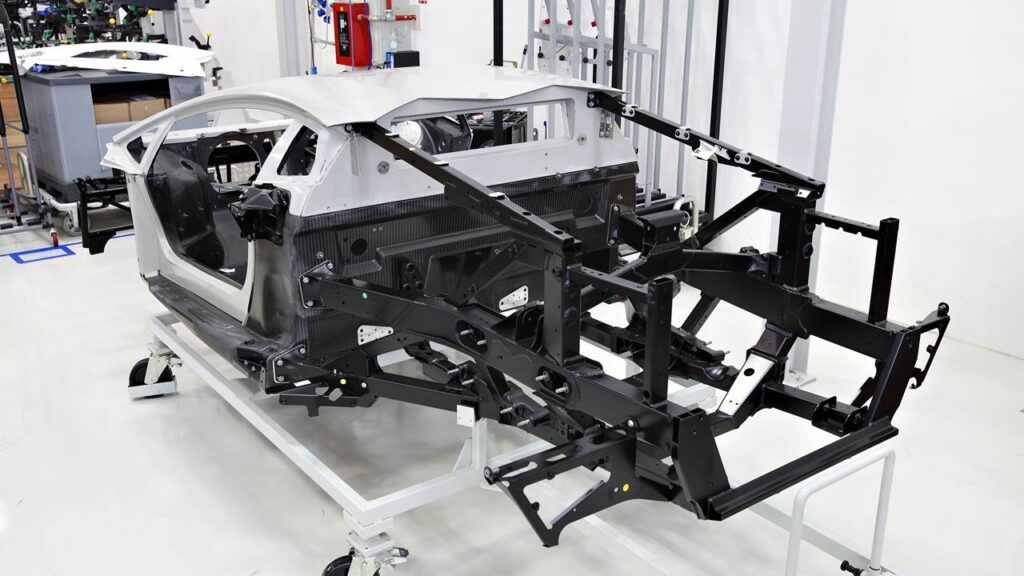
2010
W wyniku współpracy z Boeingiem i Callaway – producentem kijów golfowych – Lamborghini opracowuje technologię Forged Composites®. To specyficzny patent dzięki któremu w ciągu kilku dni powstała koncepcja supersamochodu Sesto Elemento. W tym samym roku w zakładzie produkcyjnym Lamborghini (wykorzystywanym później do produkcji monokoku Aventadora) powstaje zakład produkcji komponentów kompozytowych. Dział ten wykorzystuje także zautomatyzowaną produkcję.
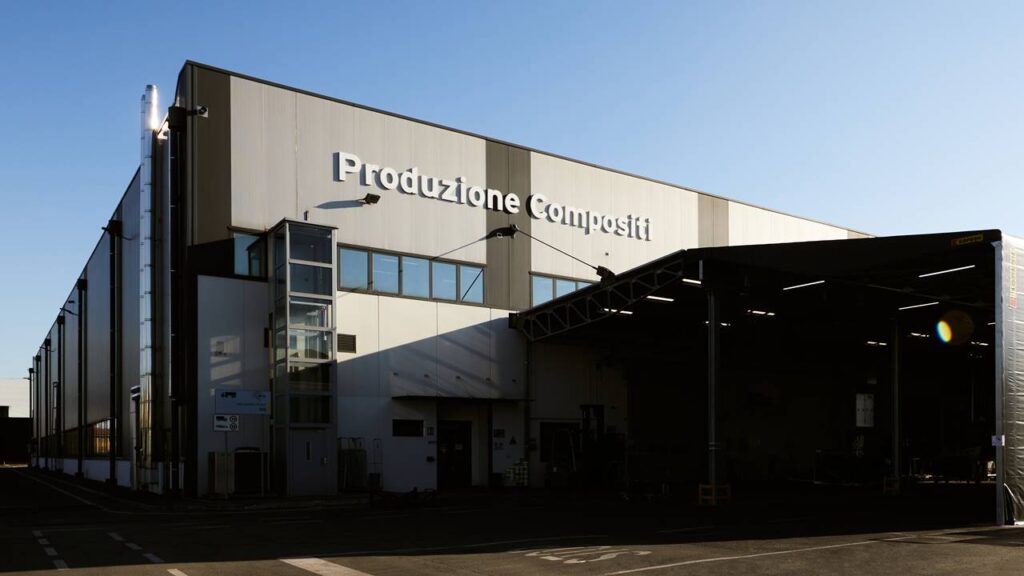
2011
Debiut nowego Aventadora LP 700-4, wyposażonego w innowacyjny monokok z włókna węglowego zaprojektowany i wyprodukowany w całości w Sant’Agata Bolognese. Nadwozie Lamborghini Aventador, wykonano w całości z włókna węglowego. Jego unikalna struktura, gwarantuje wytrzymałość oraz niską wagę nadwozia, która wynosi zaledwie 229,5 kg. Właśnie ze względu na unikalny i złożony charakter procesu stosowanego do produkcji nadwozia z materiału kompozytowego, Lamborghini decyduje się na jego produkcję we własnym zakresie.
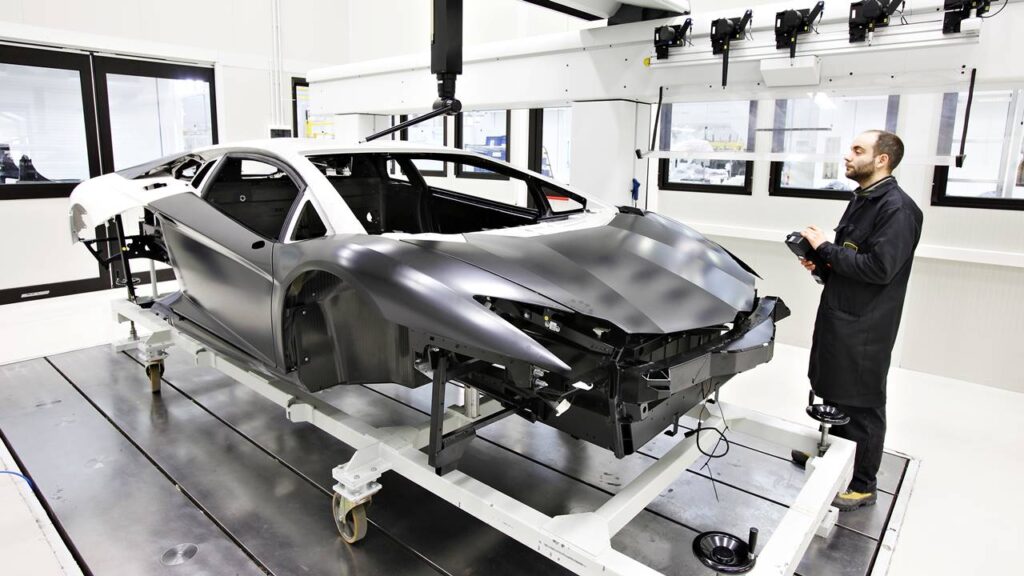
Większość części tworzących nadwozie jest produkowana przy użyciu opatentowanej przez Lamborghini technologii „RTM-Lambo”. Proces ten eliminuje potrzebę ręcznego laminowania i wykorzystania autoklawów, ale jednocześnie umożliwia stosowanie form z włókna węglowego, skracając czas produkcji i czyniąc RTM-Lambo najnowocześniejszą technologią produkcyjną. W 2011 r. rozpoczęto również opracowywanie technologii napraw poprzez nowe partnerstwo z Boeingiem.
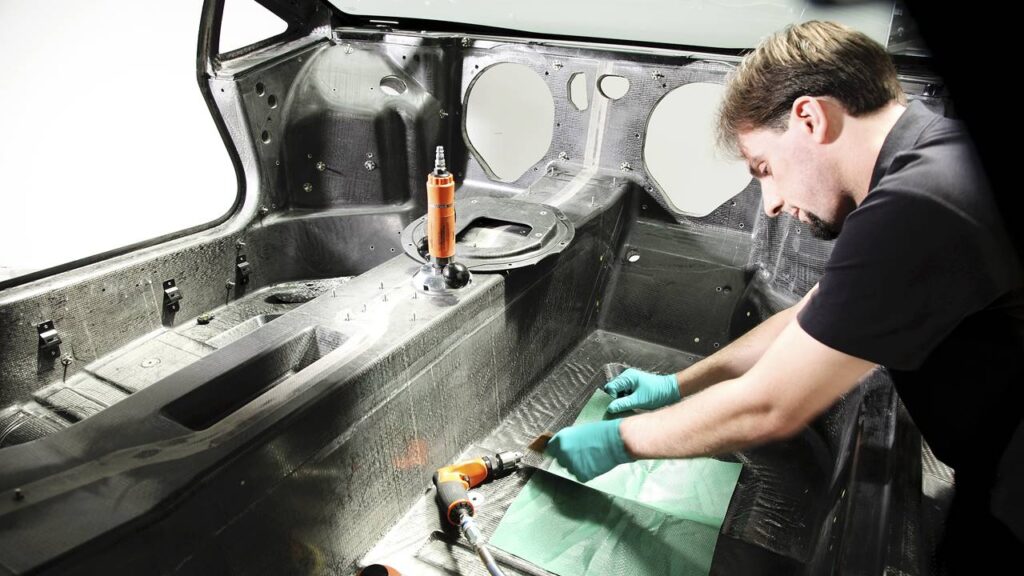
2014
Automobili Lamborghini staje się pierwszą firmą motoryzacyjną na świecie, która uzyskała certyfikat TÜV dla swojej usługi naprawy samochodów z włókna węglowego. Ta usługa naprawcza, której rozwój rozpoczął się w 2011 roku, jest kontrolowana przez ekspertów TÜV Italia i certyfikowana pod kątem jakości, identyfikowalności, niezawodności, punktualności i dokładności. Usługę świadczą mobilni specjaliści zwani „latającymi lekarzami”. Są to profesjonaliści, którzy przeszli wstępne szkolenie w Departamencie Napraw firmy Boeing Co., a następnie przeszli szkolenie w Abaris Training Resources Inc. w Nevadzie. Tam uzyskują kwalifikacje do zaawansowanej technologii naprawy uszkodzeń struktur kompozytowych, uznawanej przez Federalną Administrację Lotnictwa USA. Celem tego jest zagwarantowanie, że parametry techniczne naprawianej części będą w 100% identyczne z nowym elementem.
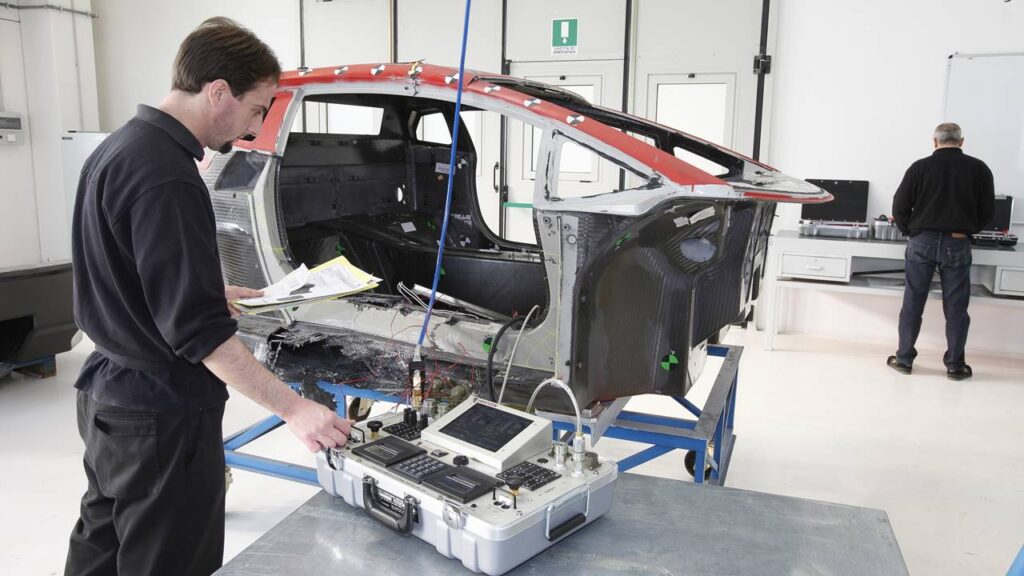
2016
Inauguracja nowego laboratorium badawczego włókien węglowych, Advanced Composite Structures Laboratory (ACSL), w Seattle (Waszyngton, USA). Działając jako podmiot zewnętrzny wobec centrali firmy w Sant’Agata Bolognese, ACSL bada wszelkie innowacje w technologii włókna węglowego.
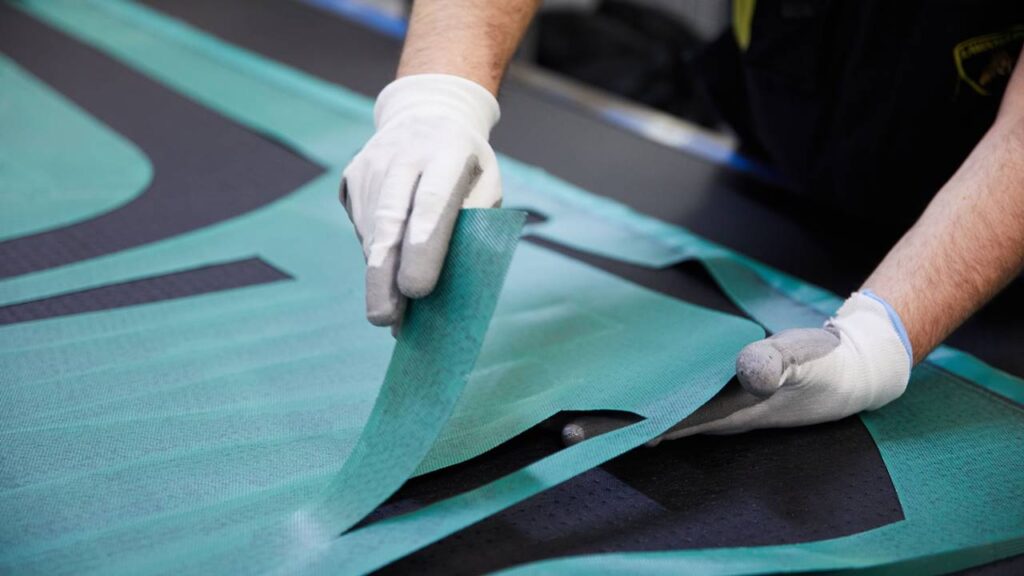
2017
Projekt badawczy z Houston Methodist Research Institute dotyczący badania materiałów kompozytowych w medycynie. Automobili Lamborghini udostępnia swoje know-how w zakresie badań materiałów kompozytowych z włókna węglowego, rozpoczynając współpracę w zakresie badań tych materiałów w dziedzinie medycyny. Projekt badawczy koncentruje się na badaniu biokompatybilności materiałów kompozytowych. Materiały te potencjalnie mogłyby zostać wykorzystane do opracowania implantów protetycznych i urządzeń podskórnych. Celem jest opracowanie nowych, lżejszych materiałów, które przepuszczają promienie rentgenowskie i są lepiej tolerowane przez organizm ludzki. Dodatkowo cechują się większą trwałością niż te stosowane obecnie w medycynie.
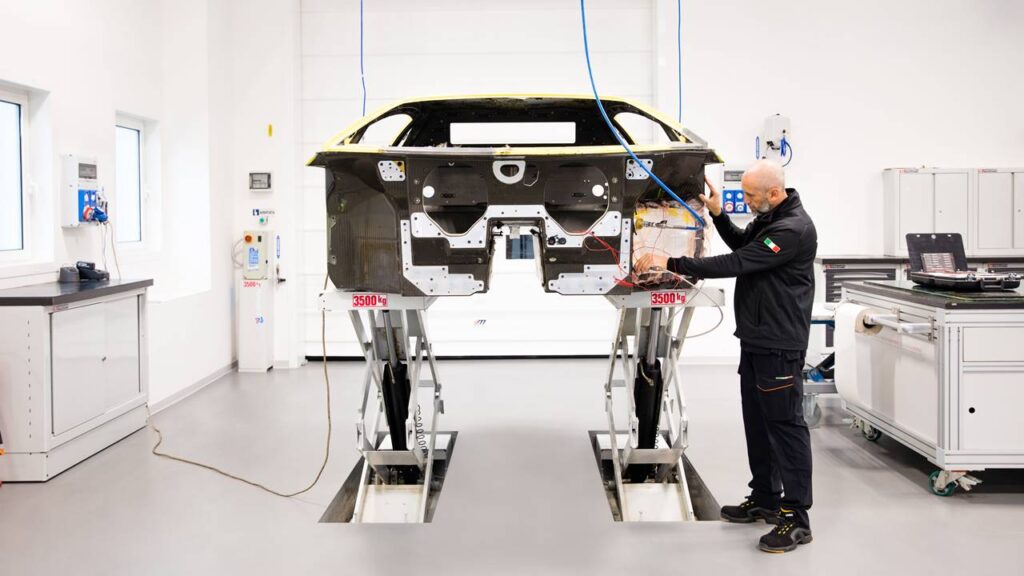
2019
Testowanie w kosmosie. Automobili Lamborghini jest pierwszym producentem samochodów na świecie, który prowadzi badania nad materiałami z włókna węglowego na pokładzie Międzynarodowej Stacji Kosmicznej (ISS). Wspólne badania nad zaawansowanymi materiałami kompozytowymi z włókna węglowego zainicjowane dwa lata temu przez Automobili Lamborghini i Houston Methodist Research Institute osiągnęły ważny moment. Wystrzelenie rakiety Northrop Grumman Antares z Wallops Flight Facility w Wirginii miało miejsce 2 listopada 2019 r. Misją było dostarczenie na ISS serii próbek materiałów kompozytowych wyprodukowanych przez Automobili Lamborghini.
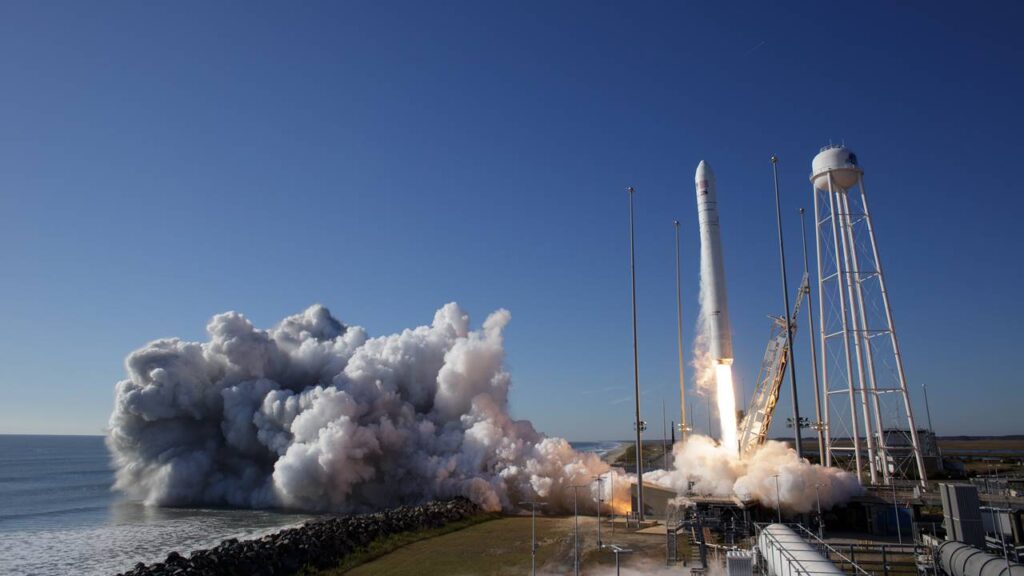
Projekt ten jest częścią programu testów sponsorowanych przez amerykańskie Narodowe Laboratorium ISS i nadzorowanych przez Houston Methodist Research Institute. W szczególności testy te mają na celu analizę reakcji pięciu różnych materiałów kompozytowych produkowanych przez Lamborghini na ekstremalne naprężenia generowane przez środowisko kosmiczne. Wszystko z myślą o przyszłych zastosowaniach w samochodach Lamborghini oraz w medycynie.
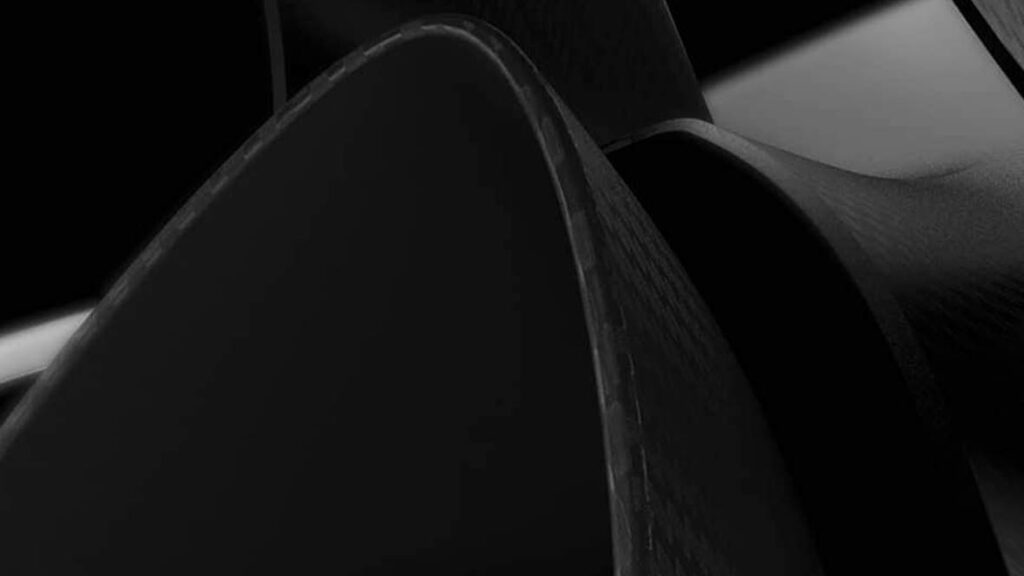
2021
Wprowadzenie na rynek Lamborghini Essenza SCV12, pierwszego samochodu z klatką bezpieczeństwa z włókna węglowego homologowaną zgodnie ze standardami bezpieczeństwa FIA Hypercar. To niezwykłe osiągnięcie jest wynikiem trzydziestoletniego doświadczenia Automobili Lamborghini w badaniu i stosowaniu materiałów kompozytowych w branży motoryzacyjnej.
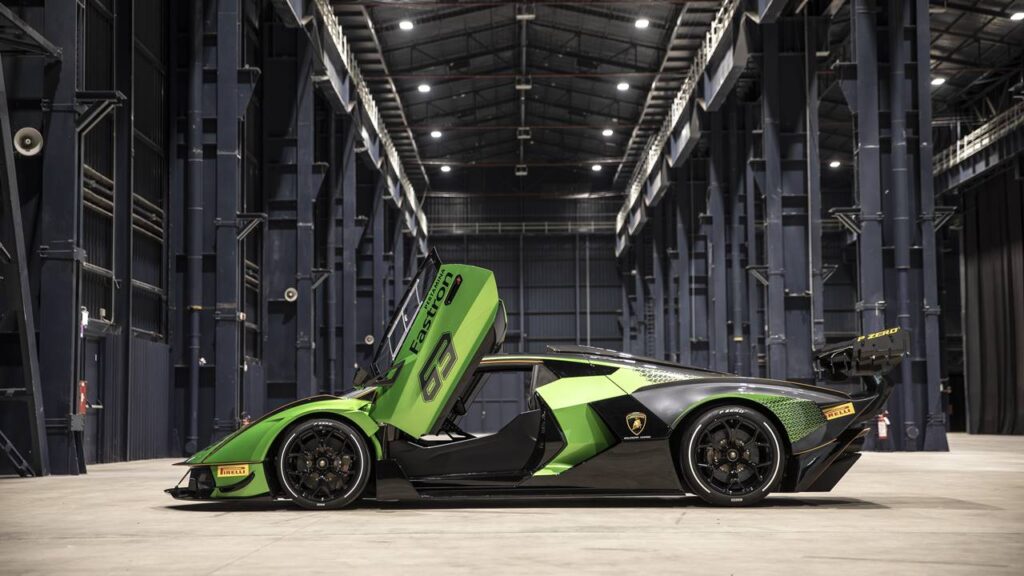
Aby to osiągnąć, nadwozie z włókna węglowego produkowane w autoklawach CFK firmy Lamborghini jest wzmacniane w kilku kluczowych miejscach. Musi bowiem wytrzymać siły przekraczające 12 ton bez znaczących deformacji podczas rygorystycznych testów statycznych i dynamicznych w celu uzyskania homologacji FIA. Istnieje ponad 20 rodzajów testów statycznych, które oprócz nadwozia obejmują także pedały, mocowania pasów bezpieczeństwa i zbiornik paliwa. Z drugiej strony dynamiczne testy zderzeniowe obejmują uderzenia z prędkością do 14 metrów na sekundę. W tego typu testach nadwozie nie może też być narażone na wtargnięcie elementów zewnętrznych, które mogłyby wejść w kontakt z kierowcą. Dodatkowo zbiornik paliwa musi zachować szczelność.
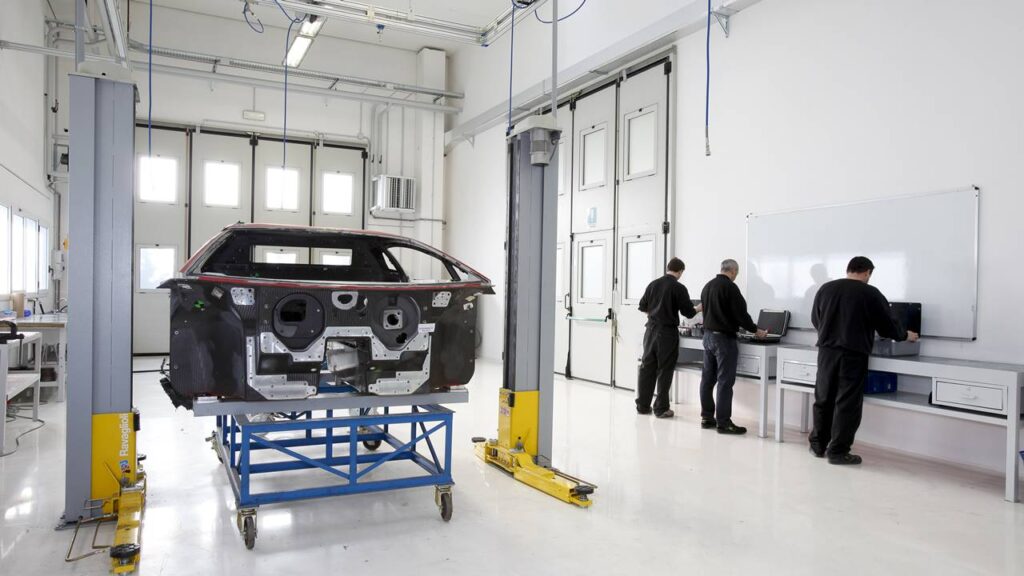
Dzisiaj
Zrównoważony rozwój i recykling odpadów. Innym aspektem, nad którym Lamborghini pracowało przez lata, jest zrównoważenie środowiskowe procesów produkcji materiałów kompozytowych. Obecnie badania i projekty podejmowane przez inżynierów Lamborghini doprowadziły do wdrożenia technologii produkcyjnych, które zmniejszają zużycie energii i zasobów, takich jak woda. Technologie te mają także na celu również zmniejszenie ilości kompozytowych odpadów produkcyjnych.
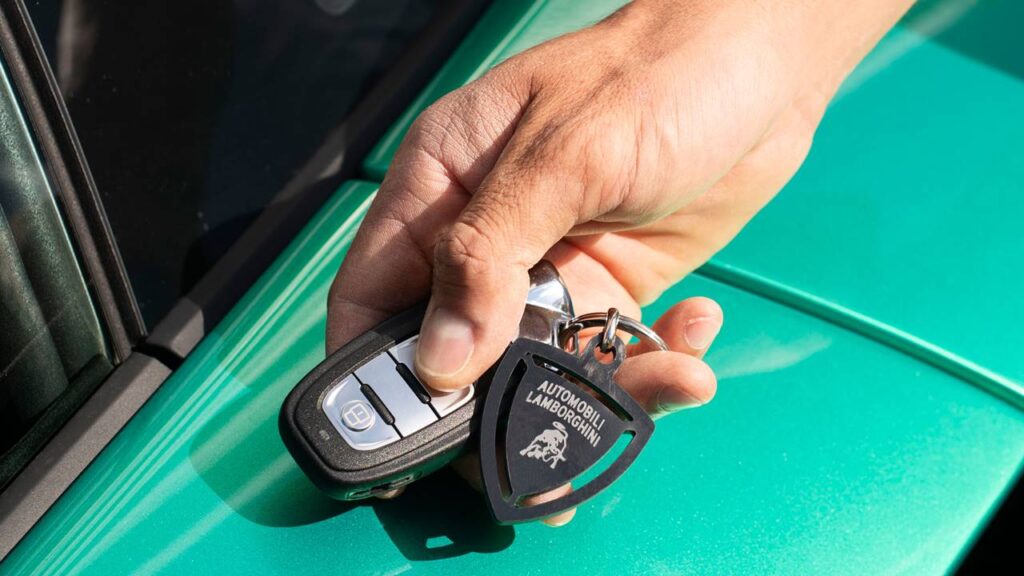
Wszystkie odpady ponownie wykorzystuje się również w innych zastosowaniach, w pojeździe lub do innego użytku w fabryce, np. do wózków. Wszystko, czego nie można ponownie wykorzystać, jest zbierane i poddawane recyklingowi w celu odzyskania włókna. Wytwarza się z niego nowe produkty z „przetworzonego włókna węglowego”. Mogą to być nawet inne części pojazdu o mniej wymagających parametrach konstrukcyjnych i estetycznych, takie jak panele podłogowe. Ponadto z odpadów poprodukcyjnych powstają produkty uboczne, takie jak produkty promocyjne dla klientów i gości podczas imprez organizowanych przez Lamborghini. Ostatecznym celem jest stworzenie całkowicie zamkniętego obiegu produkcyjnego włókna węglowego.
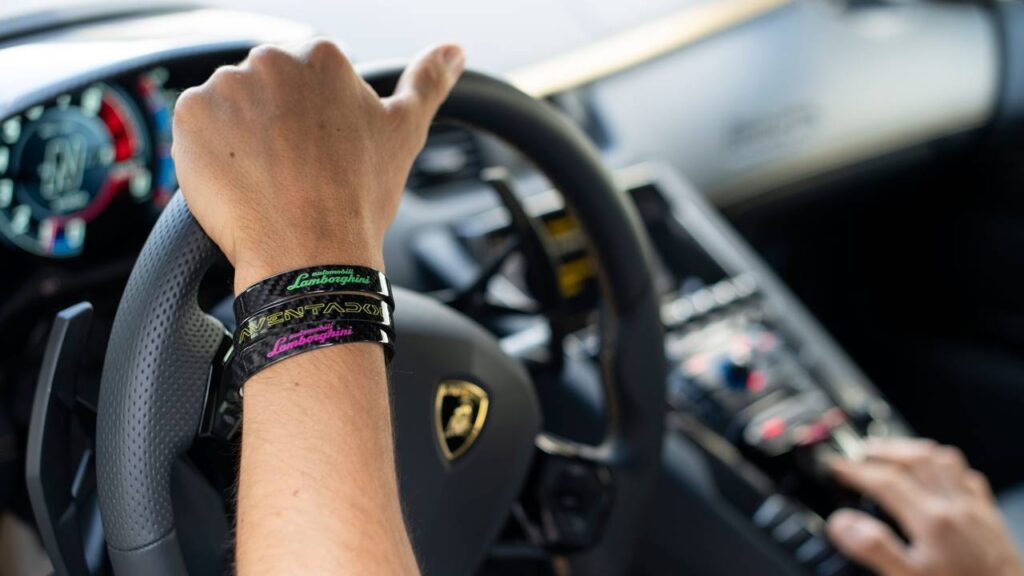
Informacja prasowa
Pozostałe wiadomości tutaj
Jeśli podoba Ci się Overdrive i to co robimy, to możesz nas wspierać za pośrednictwem serwisu PATRONITE. Uzyskasz dostęp do dodatkowych materiałów i atrakcji. Dla wspierających fanów przewidujemy między innymi: dostęp do zamkniętej grupy na facebooku, własny blog na naszej stronie, gadżety, możliwość spotkania z naszą redakcją, uczestniczenie w testach. Zapraszamy zatem na nasz profil na PATRONITE.